The Terracotta grinder will make grinding of wasted pottery items faster than the traditional mortar and pestle. It will lessen the cost of production, and will also help in solving the problem of shortage of clays.
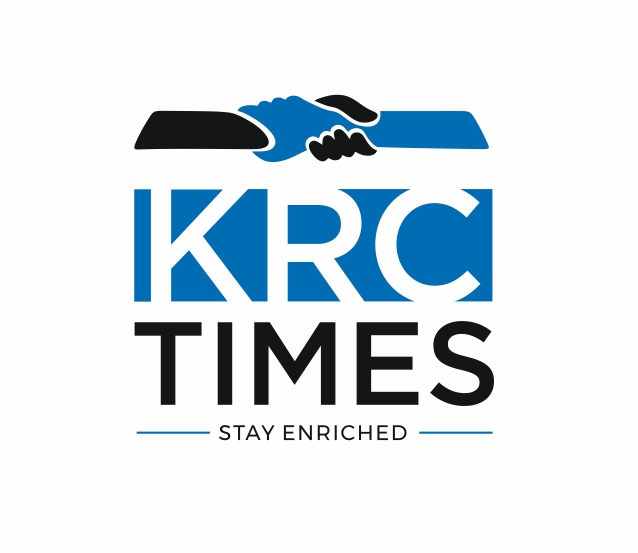

Khadi and Village Industries Commission (KVIC) launched a first ever ‘Terracotta Grinder’ at Sewapuri in Varanasi in UttarPradesh. This machine xan grind the wasted and broken pottery items which can be reused in the process of pottery-making.

Highlighting its usefulness, Vinai Kumar Saxena, Chairman, KVIC said that by mixing 20 percent of this wasted terracotta powder, the potter will make a saving of at least Rs 520.
The Terracotta grinder will make grinding of wasted pottery items faster than the traditional mortar and pestle. It will lessen the cost of production, and will also help in solving the problem of shortage of clays.

The grinder was designed by Vinai Saxena himself, the KVIC Chairman, and fabricated by a Rajkot-based engineering unit .
He also distributed 200 Electric Potter Wheels and other pottery machines among the villagers which will also meet the growing demand for terracotta products at Varanasi railway station following a direction by the Ministry of Railways to Zonal Railways and IRCTC to take urgent necessary action to ensure use of locally produced, environment friendly terracotta products like Kulhad, glasses and plates for serving passengers through all static catering units at Varanasi and Raibareilly railway stations.

Union Minister of MSME Nitin Gadkari has proposed to introduce kulhads and other terracotta products at 400 prominent railway stations where these machines will help boost productivity.

KVIC, as part of its commitment to Swachh Bharat Abhiyaan, had also started manufacturing of plastic-mixed handmade paper at Kumarappa National Handmade Paper Institute (KNHPI), a KVIC unit in Jaipur under its project REPLAN (REducing PLAstic in Nature). In this project, the waste plastic is collected, cleaned, chopped, beaten and treated for softness. After that, it is mixed with the paper raw material i.e. cotton rags pulp in a ratio of 80 % (pulp) and 20% (plastic waste). The institute has sold over six lakh handmade plastic mixed carry bags since September 2018.